Emergency! Fanuc Timeout Line Halted Production? Get Immediate Help Here! - A Critical Examination
The emergency Fanuc timeout line, a critical component in manufacturing operations, poses complex challenges that require a comprehensive understanding of technical, operational, and human factors to ensure efficient production.
Technical Complexities
-
Installing and configuring Fanuc timeout lines demands specialized technical expertise.
-
Improper settings can lead to interruptions, delays, and safety hazards.
-
Fanuc timeout lines integrate with various machines and software systems.
-
Compatibility issues can cause communication errors and malfunctions.
-
Diagnosing and troubleshooting Fanuc timeout line issues require advanced technical skills.
-
Real-time monitoring tools help identify potential problems.
Operational Challenges
-
Timeout lines play a crucial role in maintaining production flow.
-
Improperly configured lines can create bottlenecks and reduce efficiency.
-
Fanuc timeout lines require effective material handling and inventory management.
-
Insufficient material supply or inefficient inventory control can lead to production delays.
-
Operators must be adequately trained to handle Fanuc timeout lines.
-
Errors due to lack of knowledge or skill can disrupt production.
Human Factors
-
Fanuc timeout lines involve moving machinery and electrical components.
-
Proper safety protocols must be implemented to prevent accidents.
-
Operators working on Fanuc timeout lines may experience stress and fatigue.
-
Ergonomic considerations and work-rest cycles are crucial for maintaining alertness and productivity.
-
Effective communication and collaboration among operators, supervisors, and maintenance personnel are essential for troubleshooting and resolving issues.
-
Clear communication channels and established response protocols are critical.
Perspectives and Scholarly Research
-
Engineering research focuses on optimizing Fanuc timeout line configuration and performance.
-
Studies have shown that proper installation and maintenance can significantly reduce downtime.
-
Operations management research examines the role of Fanuc timeout lines in production flow optimization.
-
Findings suggest that integrating these lines effectively improves efficiency and reduces waste.
-
Psychology and ergonomics research explores the impact of Fanuc timeout lines on operator safety and well-being.
-
Studies indicate that ergonomic modifications and training can enhance operator performance and reduce fatigue.
Implications for Manufacturing Operations
-
Investing in training programs and advanced monitoring technology can mitigate risks and improve line efficiency.
-
Establishing clear communication channels and fostering collaboration among staff ensures timely troubleshooting and problem-solving.
-
Regularly evaluating Fanuc timeout line performance and implementing continuous improvement measures can optimize production and reduce downtime.
-
Considering human factors in Fanuc timeout line design and operation promotes operator safety, reduces fatigue, and enhances productivity.
Conclusion
The 275 X 1.075 Mystery Solved! Experts React.
HBD Mode Driving You Crazy? This Fix Works Every Time
Unlock Fooocus Performance: Master Your Error Logs Today
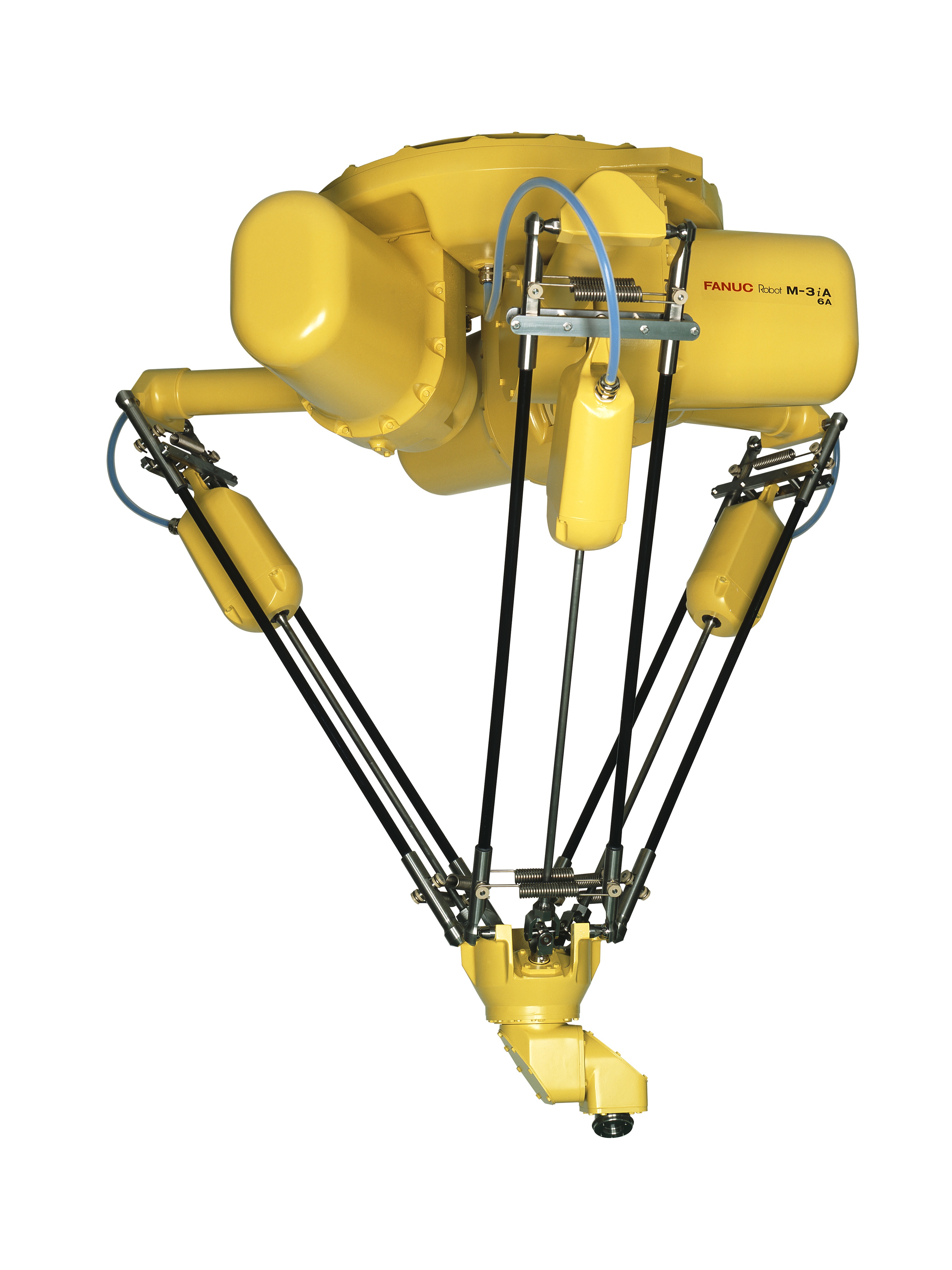
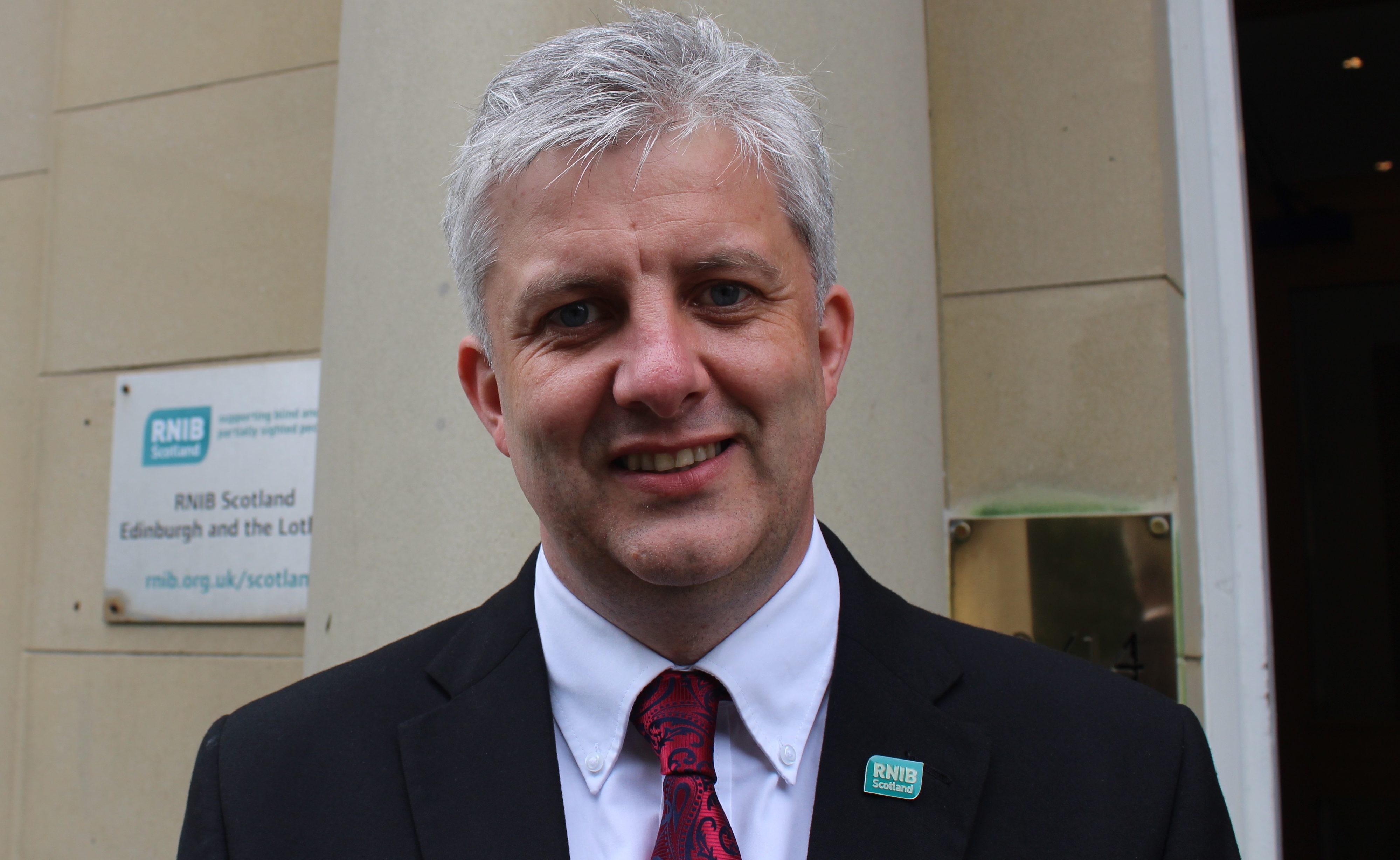